Sustainable Design, Construction and Management – For a Green Construction Industry
The construction industry is one of the most resource-intensive sectors of the economy. Demand for housing is also continuously increasing. Accordingly, the construction industry is challenged to use raw materials and energy more efficiently.
Lesezeit: 12 min
Publiziert am: 30.05.2023
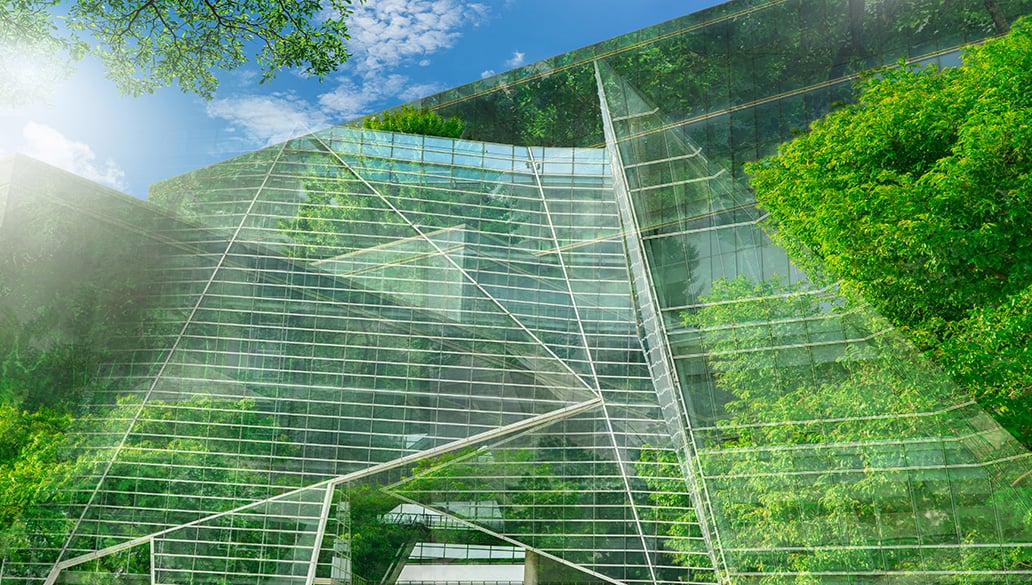
Nieder mit den Datensilos, hin zum digitalen Gebäude-Ökosystem mit offenen Standards: Dieser Paradigmenwechsel beschäftigt die Bauindustrie seit Jahren. Ebendiese Vision verfolgte Professor Georg Nemetschek bereits bei der Gründung seines Ingenieursbüros im Jahre 1963 – und verwirklicht die Nemetschek Group mit ihren starken Marken heute und in Zukunft.
Anfänge der Digitalisierung in der Bauindustrie
1984 – drei Jahre nach der Einführung des ersten IBM Personal Computers – führte die damalige Nemetschek Programmsystem GmbH die objektbasierten Systeme ALLPLAN sowie ALLPLOT ein. Diese Systeme, wie auch später ARCHICAD, gingen einen großen Schritt weiter als andere verfügbare 3D-CAD-Systeme dieser Zeit. Sie versetzten Architekt*innen und Ingenieur*innen erstmals in die Lage, Skizzen am Computer zu generieren, zu bearbeiten und digital mit anderen Stakeholdern zu teilen.
Auch wenn die ersten Digitalisierungstools einige Prozesse im Bauwesen vereinfachten, generierten Datensilos aufgrund mangelnder Interoperabilität der Softwaresysteme so manches an „Handarbeit“ beim Transferieren der Daten. Dieses Schnittstellenproblem band nicht nur personelle Kapazitäten, sondern öffnete auch Flüchtigkeitsfehlern Tür und Tor und verzögerte Prozesse. Infolgedessen sprengten Bauprojekte häufig den Budget- und Zeitrahmen.
Gefragt war eine gemeinsame „Sprache“ im Bauwesen. Als Garant eines lückenlosen Informationstransfers erleichtern einheitliche Datenformate die Kollaboration entlang aller Projektetappen, verhindern Datenverluste sowie Fehler und stellen die langfristige Nachvollziehbarkeit von Bauprojekten sicher.
Geburtsstunde des BIM
Der holistische Daten-Ansatz manifestierte sich 1999 in der Plattform O. P. E. N., ersonnen von Professor Georg Nemetschek: Das seit 1993 erdachte datenbankgestützte System schlüsselte Bauwerke in semantische Bauproduktmodelle für den Zugriff durch verschiedene Softwaresysteme auf. O. P. E. N. lagen dieselben Strukturen zugrunde wie den späteren International Foundation Classes (IFC) der gemeinnützigen Organisation BuildingSMART: offene, neutrale, international anerkannte XML-Datenformate für Bauprojekte. Das Entstehen der International Foundation Classes (IFC) gilt auch als Geburtsstunde von BIM (Building Information Modeling).
2012 folgte ein weiterer Meilenstein auf dem Weg zur Harmonisierung der Datenwelten im Bauprojektlebenszyklus. Gemeinsam mit buildingSMART International und führenden Softwareanbietern rief Nemetschek die OPEN-BIM-Initiative ins Leben mit der Mission, alle relevanten Daten zu einem Bauwerk mittels herstellerunabhängiger Standardformate in die 3D-CAD-Modelle von Bauwerken zu integrieren. Neben der architektonischen Struktur lässt sich das Gebäudemodell so mit vielen wertvollen Informationen und Kalkulationen anreichern, beispielsweise für die kaufmännische Planung oder das Facility Management. Dank dieser ganzheitlichen Betrachtung eines Gebäudes oder einer Infrastruktur als dynamisches Ökosystem lassen sich neue ökonomische und ökologische Potenziale entlang des gesamten Lebenszyklus intelligent ausschöpfen.
Vom Gebäudemodell zum Digitalen Zwilling
Gebäude und Infrastrukturen sind deutlich dynamischer, als man es auf den ersten Blick vermuten würde. Sie entwickeln sich stetig weiter, nicht nur auf der Datenebene, sondern auch auf der handfesten physischen Ebene. Umbauten während der Nutzungsphase lassen die Schere zwischen dem digitalen Modell und der gebauten Realität des Gebäudes immer weiter auseinanderklaffen. So wird es zunehmend schwieriger, auf Basis des ursprünglichen digitalen Modells zukunftsgerichtete Entscheidungen zu treffen.
Um die Schere zu schließen, muss der Ist-Zustand des Gebäudes mittels Reality-Capture-Technologien erfasst, semantisch verknüpft und mit dem 3D-CAD-Bauplan abgeglichen werden. Aus diesen Informationen sowie Echtzeit-Sensordaten, beispielsweise aus dem Gebäudeautomationssystem, lassen sich seit Oktober 2023 mit der cloudbasierten, offenen Plattform der Nemetschek Group dTwin Digitale Zwillinge von Gebäuden errichten. Digitale Zwillinge liefern eine objektive und interaktive Basis für Entscheidungen entlang des gesamten Gebäudelebenszyklus. Ein weiterer wichtiger Meilenstein im Ansatz „Denken im Ganzen“.
Heute, nach mehr als 60 Jahren Pionierarbeit und Vorreiterrolle, vernetzt die Nemetschek Group mit ihrem umfangreichen Portfolio alle Bauphasen, Gewerke und Stakeholder auf der ganzen Welt. Mit den innovativen Digitalisierungslösungen arbeiten über sieben Millionen Menschen weltweit erfolgreich und effizient an Bauwerken und Infrastrukturobjekten der Gegenwart und der Zukunft. Sei es in der Planung, in der Bauphase oder im Gebäudebetrieb – mit offenen Schnittstellen, technischer Expertise und Know-how treibt Nemetschek als Schrittmacher die interdisziplinäre Kollaboration im gesamten Baulebenszyklus voran. Wenn innovative Software und offene Standards Reibungsverluste zwischen den einzelnen Phasen des Gebäudelebenszyklus eliminieren, wird der komplette Bauprozess termintreuer, effizienter, wirtschaftlicher und nachhaltiger. Vom Denken im Ganzen zum Bauen im Ganzen.
A Typical Sequencing Conflict Arises
Designers require on-site teams to install metal framing according to specifications and BIM models for technical services. Fire-rated wall stud installation involves framing encasing boxes around openings for specified technical installations, ensuring a proper fire seal. On-site teams, however, need coordinated planning to finalize technical MEP/HVAC layouts before partition walls are erected. Ideally, openings should be prepared before installing technical services, demanding accurate overlay of service layouts on partition drawings. This is seldom done, as design teams often optimize layouts during coordination, impacting metal wall stud placement. This sequencing challenge poses a significant project risk, particularly when fire partition walls are closed from both sides, hindering visibility. Damage to wall studs during later installations can compromise the wall's fire integrity.
Checking Work Quality of Fire Rated Wall Installations with Imerso AI
Imerso empowered Nyt Hospital Nordsjælland's construction team to boost their site supervision 15-fold by enabling them to independently conduct 3D scanning activities, a task traditionally deemed time-consuming and requiring expert surveyors. The Imerso platform analyzes the on-site As-built environment against BIM models, promptly reporting work status and deviations. Project Manager Anders Kaas prevented numerous costly issues within months, surpassing expectations. Additionally, Anders's team achieved precise on-site monitoring of fire-rated wall stud installations with Imerso, ensuring millimeter-accurate placement. Swift comparisons with BIM plans identified potential issues, promptly addressed to enhance building safety through efficient routine work status monitoring. Read the first 16 months' results here.
Combining Better Design Controls with Onsite Quality Checks
Another typical fire-stopping challenge in construction projects lies in the installation of technical equipment through wall openings in the concrete superstructure. To preserve fire-stopping capabilities, such equipment must be installed at specific distances from the structure and between each other, to allow appropriate fire-rated insulation.
The popular BIM coordination software Solibri, an industry-leading tool and partner of Imerso, recently launched new rulesets for validating safety-compliance automatically in the BIM models. But even in projects leveraging these accurate models, the problem happens when the onsite installations deviate from the planned design and remain undocumented, since traditional manual and visual controls using photos, 360° panorama images, and manual checklists are ineffective at flagging such changes. By analysing the onsite installation status against the BIM plans, Imerso helps the Nyt Hospital Nordsjælland team to prevent such hidden deviations from being overlooked, by detecting them instantly without human subjectivity.
Sustainable Building Management
Around 80% of the costs of a building are incurred during the utilization phase. A large part of this expenditure is due to energy consumption. Digital tools help monitor and reduce this energy consumption – as well as enable optimal control of heating, ventilation, and lighting. They can also be used to plan and use existing office space efficiently by showing how much space is actually needed, saving resources.
Seeing Change as an Opportunity
The healthcare sector is facing a number of challenges worldwide in terms of operating real estate. On the one hand, the demand for new assisted living facilities and nursing homes is continuously increasing due to demographic changes. On the other hand, many governments are placing greater emphasis on implementing sustainability and reducing energy consumption when operating a care facility.
The care organization "Stichting Voor Regionale Zorgverlening" (SVRZ) in the Zeeland region of the Netherlands is also facing up to these challenges. It primarily cares for vulnerable elderly people who need short- or long-term care and support due to their physical condition or impairments caused by dementia, for example. With more than 57 care facilities spread over 23 centers in the Zeeland region, SVRZ faces major challenges in maintaining its existing properties. This is one of the reasons why this area is the responsibility of an independent department, which has been using the Spacewell Maintenance solution for multi-year maintenance planning since 2012.
In 2020, the Energy Transition Master Plan was adopted by SVRZ with the subtitle: "Full speed ahead to zero gas". SVRZ has a sustainable goal and ambition to operate its care properties completely gas free by 2030. If this ambitious goal could be realized, SVRZ would meet national climate goals for 2050 before 2030.
Since then, the organization has already installed more than 6,500 solar modules. In the process, the technical condition of the roofing was checked in advance using the multi-year maintenance plan. At several sites, where necessary, the roof covering was renewed before the solar panels were installed, which increased the insulation value to the level of current standards for new buildings.
SVRZ also applied the principle of natural replacement time to renovations: for example, conventional light bulbs were replaced with modern and energy saving LED lighting as standard as part of renovation activities, and existing gas boilers were replaced with electric heat pumps.
As a result, SVRZ achieved a CO2 reduction of no less than 28% in the 2018-2020 period and reduced fossil natural gas consumption by more than 400,000m³ per year. In the coming years, the implementation of the Energy Transition Master Plan will continue based on the sustainable multi-year maintenance plan.
(c) Groepswoning ter Schorre
The Office of the Future
The science and technology company Merck has its corporate headquarters in Darmstadt, Germany, and employs more than 60,000 people in over 60 countries worldwide. In Germany alone, more than 12,000 employees work to find solutions to some of the greatest medical challenges of our time.
As is common in many companies, every employee in the company used to have a fixed assigned workstation. New ways of using workstations and space have been explored – but a strategic approach to hybrid working and the office of the future only recently received a significant boost due to the COVID-19 pandemic.
In order to make the company headquarters fit for the work of the future and to allow all employees to participate in a modern office concept, Merck relied on the implementation of workplace solutions from CREM SOLUTIONS for the redesign of the working environment. The maxim of the concept was to get away from fixed workplaces and towards "New Work" or "Activity Based Working". As part of the redesign process, the Workplace Solutions system enabled a meaningful analysis of space and workspace utilization and ensured a safe return of employees to the office, especially during the COVID-19 pandemic. Quantitative, data-based monitoring of occupied space is also possible. The main goal here is to proactively manage available space and be able to respond in real time to changes in the organization as well as user behavior.
The information collected with the Workplace system is extensively analyzed and used for future scenarios in order to drive the further digitalization of the company's buildings and offices and implement modern working methods. Efficient control can optimize both the use of space and energy consumption – for example, it is no longer necessary to heat all office areas across the board or provide permanent lighting. Based on sound planning, accumulated experience, and close collaboration between the project teams, the Workplace solutions and the integrated Internet of Things (IoT) solutions were designed in such a way that the desired needs of the Merck Group are easily and completely mapped in a smart building system. In the long term, the aim is to deploy the Workplace system across the board in suitable properties.
(c) Tobi Bohn Fotografie
A Circular Construction Industry
The project examples show that there is a shift in thinking in the construction industry: away from analog silos and toward digital collaboration. This rethinking is also driven by the need to plan, build, and operate more sustainably. With the help of digitalization, this cycle can be closed from initial planning to the end of the life cycle – for a more sustainable, future-oriented construction industry.
Register For Our Newsletter Today
Stay up-to-date and be the first to know about our latest article releases on Nemetschek Topics & Insights
SubscribeContacts
Senior Director Group Communications & Corporate Responsibility