Transparency and time savings
123onsite supports the use of machines, materials and employees
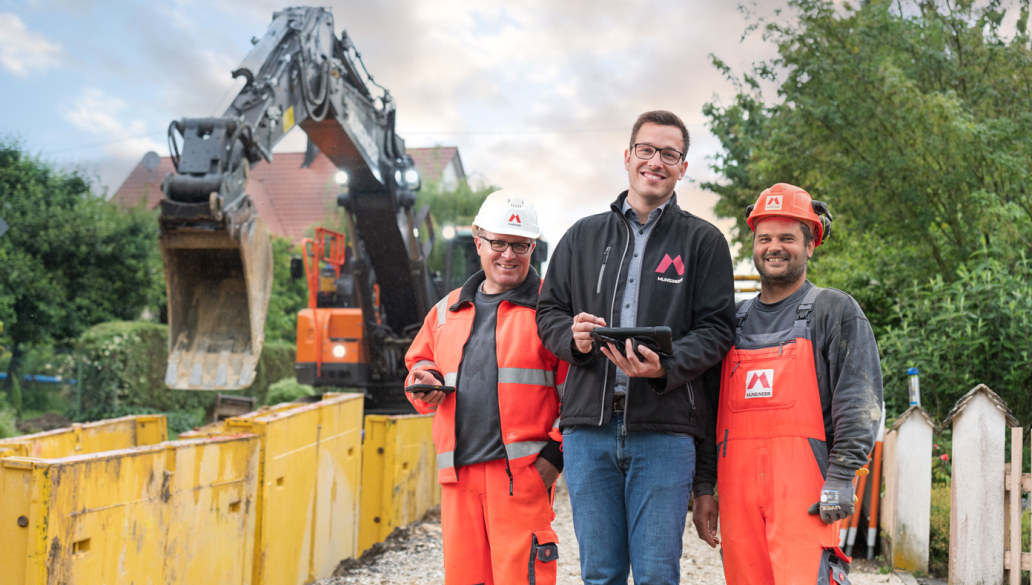
Facts
Location
Blossenau, Germany
Nemetschek Group Brands
NEVARIS
Sector
Civil engineering
Client
Münsinger Erdbau GmbH
Technology used
123onsite
The family-run company Münsinger Erdbau GmbH from Blossenau in Bavaria covers a broad spectrum in the field of civil engineering and likes to break new ground. "We are always one step ahead in the technical field, also in terms of optimised solutions in the working area," junior boss Johannes Münsinger explains. He wants a powerful and flexible time tracking program for the many special solutions the company offers. The company found what it was looking for with 123onsite, the mobile construction site management software.
The company, founded in 1952 in the rural town of Blossenau, focuses on water pipe, sewer and pipeline construction and uses earthworks to design industrial estates, new development areas, paths, roads, biotopes and bodies of water. In addition, the medium-sized company wires both under and above ground and ensures a functioning energy supply in private houses, industrial estates and urban and local districts. Transport services of material, machinery, gravel, sand or bitumen in thermo barrels are also part of the family business’ portfolio. Its customers mainly include public-sector clients and larger commercial enterprises within a 50-kilometer radius. However, Münsinger also works for private clients.
Flexible software wanted
At the beginning of the 2000s, Münsinger had a scheduling programme developed that flexibly covered both long and short assignments. However, it was not developed any further. Johannes Münsinger, M.Sc., who runs the business together with his father Dipl.-Ing. (Univ.) Ernst Josef, had all relevant time recording systems presented to him in 2017. The decision was made in favor of the mobile construction site management software 123onsitedue to its comprehensive functionalities.
At Münsinger, the appreciation of the 70 employees is a top priority. That is why making work easier for employees and improving the information exchange between the office and construction sites are particularly important. In addition, the company attaches great importance to the consistency of the data from recording to accounting to wages. Thus, the data interfaces configured by 123onsite have made it possible to achieve considerable increases in efficiency in the day-to-day running of the office.
Johannes Münsinger, managing director and civil engineer
"123onsite was the most advanced in the functions relevant to us, such as time tracking, planning and recording of construction equipment and materials, and photo documentation."
All employees equipped with smartphones
Münsinger equipped all commercial employees with smartphones on which the 123onsite app has been installed. While the employees reacted sceptically to the new way of working at first, they are now happy that they no longer have to write timesheets and can find out about their assignments at any time. Today, everyone logs into 123onsite when they start to work, logs in at the construction site and books their attendance time. The system completes the recorded hours using the stored information. The software transfers the resulting results to a server in real time.
The company did not have to change its time recording concept, instead the program adapted to the way it worked. Münsinger stored the individual company agreements in the rule designer. These can be company-internal supplements for overtime, Sunday, holiday and night work, meal allowances, but also allowances for travel, seasonal short-time allowance, weather-related absenteeism and other expenses and absences. The employee simply books his attendance time at the construction site and the system supplements the recorded hours with the information stored in the rules. Johannes Münsinger: "In the office, it can be checked via GPS whether the stamping of the activities is plausible and whether the construction site is the right one. If this is the case, the data is transferred to payroll accounting."
Recording machines and materials
If, in most cases, companies only use time tracking for the time being, the construction company has also documented the use of the construction machines and equipment as well as all materials transported by the trucks from the very beginning. For the latter, the drivers record the transported materials with delivery note number, supplier and material type.
123onsite offers two options for recording the construction machines. If the equipment is on a construction site for the whole day, Münsinger generates a daily flat rate with the previously stored data. Of course, the equipment can also be charged by time. Johannes Münsinger explains: "On construction sites, it happens again and again that residents ask if we can briefly knock down a wall or do some earthmoving in the garden." These times are quickly entered using the app. The employees at the head office use GPS tracking to check whether the device was logged on to the right construction site and then transfer the data to the invoicing program.
Fast invoicing
In order for this to work, Münsinger had an interface programmed for its in-house developed operational accounting and invoicing program, so that the complete equipment and material data can be transferred for invoicing purposes at the push of a button. The great advantage of this is that, on the one hand, no transmission errors occur, plausibility checks are carried out quickly and invoicing takes place promptly. The company also uses the data for post-calculation of the projects.
Johannes Münsinger, managing director and civil engineer
„The 123onsite software is an important building block for us on the way to the digital construction site.“
Processes successfully optimized
During the introduction of 123onsite, the civil engineer rethought, standardized and streamlined all processes. This led to time optimization. Today, the detailed preparation of individual construction sites with the corresponding deployment planning of employees, construction machinery and equipment is an essential component from which the managing director benefits. Münsinger also saves himself a trip or two to the construction site, as he can log in from the office as well as from home in the evenings and keep up to date on the construction progress with the help of the photo documentation.
Improved communication and more flexible planning
Thanks to 123onsite, the employee is significantly better informed today. Not only can he check his work schedule, but he can also see which equipment is scheduled for which construction site. If, for example, he needs a wheel loader at short notice that is located on another construction site, he simply asks the foreman.
Since Münsinger has construction sites that last several months as well as many construction sites that only last one or several days, the managing director creates a rough preliminary plan and plans the next weeks assignments in detail at short notice. The 123onsite app proactively informs the employees about this in real time. For this, the employee receives a push notification and can open the planning entry. The construction site is stored there with its geo-coordinates. If desired, Google Maps opens to navigate the employee to the construction site by vehicle.
Münsinger wants to continue to be a pioneer in the region with the 123onsite software package. "By pushing digitalization, we position ourselves in the region as an attractive employer and reliable business partner."