Everything under control
Thanks to software from 123onsite
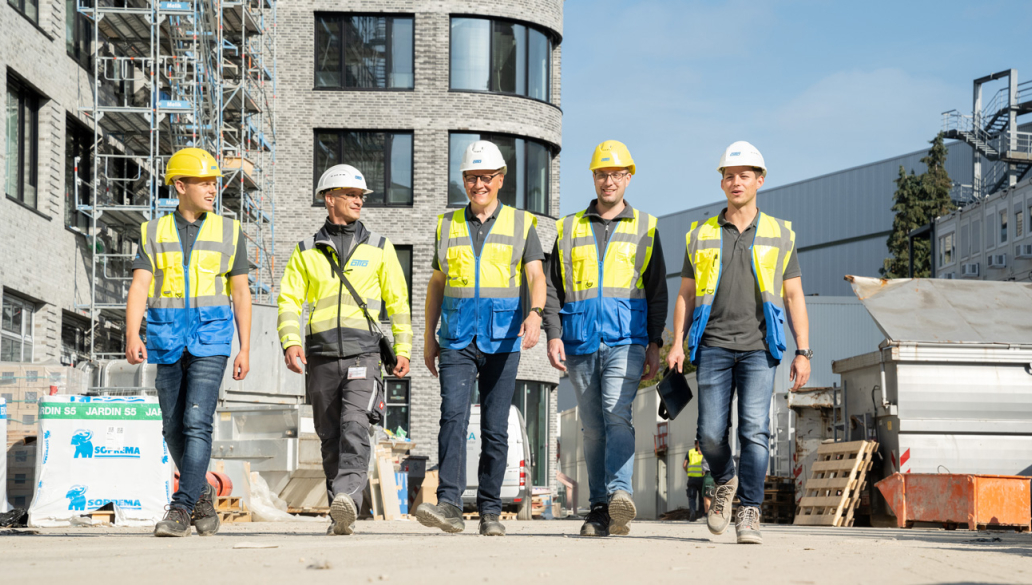
Facts
Location
Bad Berleburg, Germany
Nemetschek Group Brands
NEVARIS
Client
Otto Building Technologies GmbH, specialist for building services engineering
Technology used
123onsite
The functionalities of 123quality can now be found in the quality module.
Otto Building Technologies GmbH, a specialist in building services engineering, was looking for easy-to-use time tracking software for its 15 sites. In addition, they needed an overview of their employees' work schedules so that they could see at any given time who was on which construction site. The Westphalian company with headquarters in Bad Berleburg decided on 123onsite.
Since its foundation in 1967, the medium-sized company for sophisticated concepts and solutions in the fields of ventilation and air-conditioning technology, refrigeration technology, building automation and electrical engineering has grown steadily. Today, 900 employees provide customized building technology concepts. The customer base includes manufacturing companies as well as hotels, shopping centers, museums, universities, hospitals, administrative buildings and opera houses.
In 2015, project manager Matthias Faust, responsible for installation management at the Cologne branch, was looking for time tracking software and came across the programof the software company 123onsite from Lohne through an extensive internet research. The project manager explains: "123onsite was state of the art and exactly covered our requirements for time recording, photo documentation and reporting." Previously, the monthly reports were written by hand by the installers or partly created via an Excel spreadsheet. Processing them was a lot of work for the HR department and was also prone to errors. With 123onsite, times, expenses and absences are now recorded digitally and can thus also be processed directly.
Matthias Faust, project manager
„123onsite was state of the art and covered our requirements for time recording, photo documentation and reporting exactly.“
Successive introduction
Matthias Faust and Steffen Schmidt, Head of IT and Occupational Safety, tested the program intensively. Afterwards, they instructed their colleagues at the Cologne branch in the use of the software by means of a pilot project. After six months, it was decided to gradually integrate other locations. Today, the installers, the construction and project managers, the designers as well as the administrative staff all use 123onsite to record their times.
The system is also used to record expenses and apply for leave. In the case of sick leave, either the supervisor or the team assistant enters the reported times. The assembly supervisors check the hours and expenses entered by the employees for the previous month and then approve the data for the personnel department. If the employees in the HR department currently still enter the hours manually into the payroll program using an Excel export from 123onsite, in future the data transfer will take place automatically via an interface.
Important for Otto
It is important for Otto to be able to assign its own employees as well as those of subcontractors to projects. This makes it possible to see who is working where, when and on which construction site at any time, as well as the workload of colleagues.
If there are any changes, the app informs the relevant employees via push message. In this way, not only long-term assignments but also short-term changes are documented in a time-saving and audit-proof manner and communicated with the respective persons.
Defect and quality management integrated
Otto works with a total of 720 licenses of 123onsite. In 2020, the company expanded the system to include the defect and quality management app 123quality and acquired 100 licenses of it. The solution is integrated into 123onsite and only had to be activated for the relevant users.
The advantage is obvious
Master data only needs to be created once, is maintained centrally and users can access the entire data pool from both applications.
With 123quality, the user quickly photographs a defect and speaks on the mobile phone what needs to be done. He locates the tasks on the digital construction plan and assigns them to the responsible employee or subcontractor with just a few taps. Different types of tickets such as tasks, defects, file notes, obstructions or performance determinations are created quickly this way. The entire process of digital defect recording, tracking and rectification is thus standardized, documented in a clearly comprehensible manner and leads to significantly better quality in execution.
Photo documentation and reporting
Every day, the colleagues on the construction site document the construction progress, but also any obstructions caused by other trades, by photo and comments. The latter is immediately forwarded to the client. This simplifies the documentation immensely, because all photos and related information are automatically assigned to the relevant project, construction area and component. To ensure that all information is included in the daily construction report, the medium-sized company had an individual report programmed by the software company. The information entered in 123quality is transferred to this report, so that the daily tickets are also included for documentation purposes.
The building services experts place photos of the defects on the corresponding floor plans. Site manager Sebastian Garbotz comments: "I forward the ticket to the subcontractor with the order to work off the defect, and I don't have to meet with him on site."
Sebastian Garbotz, construction manager
"The subcontractor sees immediately where he has to take action and we save a lot of time with this procedure."
Project manager Matthias Faust also uses 123quality to support the preparation of quotations for supplementary work. To do this, he takes measurements and special features on site, photographs the situation and adds individual comments to the information. This information helps Faust to prepare the offer. Based on the photos, he has the localities in front of his eyes.
Transparent construction reports
Since the introduction of 123onsite's solutions, the reporting process has improved significantly. The entire time recording as well as the checking of the entries are much easier. In the past, the photos were sent thorugh WhatsApp or by e-mail and had to be stored in the correct folder on the computer. Now, the photo is available with categorization, local assignment based on the construction part and the construction area with text, date and time and is automatically inserted into the construction day report.
At Otto, they appreciate the integration of both solutions.
Since the user interface of both solutions is the same, employees do not have to familiarize themselves with a second system and only have to remember their username and password once. The advantages result from the digitalization of the time recording process as well as the entire documentation. Transparency, time savings, better utilization of construction sites as well as clear and informative daily construction reports reduce enquiries.
Another advantage that should not be underestimated...
The Otto employees can use the time saved for their original activities and are thus significantly more productive than before. Due to the well-documented quality management and the fast forwarding of defects to be remedied, they can be dealt with quickly. This is an advantage that should not be underestimated in tightly scheduled and complex projects.